Constructing the neck starts with facing, jointing, and thickness
planing the rough mahogany stock. Pictured here is the thickness
planing. |
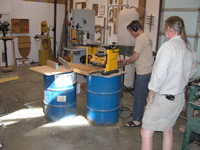 |
Shown is the target--roughing in the neck, including the head (the
"bent" portion above the neck). The head is cut from the neck stock
by cutting a "scarf joint", which as an acute angle joint. |
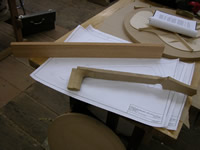 |
Here, Dan Biasca is demonstrating the use of the bandsaw to cut
the scarf joint. |
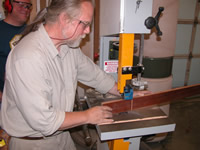 |
Once the scarf joint is cut, the two angular surface are aligned
and planed. This will create a tight glue joint. |
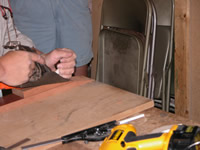 |
Using two glue blocks to spread the clamp pressure over the thin
scarf joints, the two pieces are joined together to form the angular
head. |
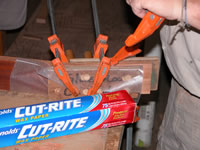 |
Finally, once glued together, the face of the head is cleaned up
using the plane. |
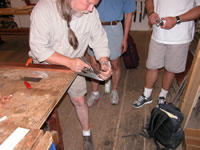 |
At this point, the neck and head are dadoed with a groove to accept
the truss rod. The cut is made by making an initial cut with a standard
saw kerf, then the neck is turned around and passed against the
fence on the other side. The width of the two cuts is measured, and
increased if necessary to widen the dado to the width of the truss
rod. This process continues, sneaking up on the final dimension by
increasing the width between the saw and the fence about 1/32" at
a time. |
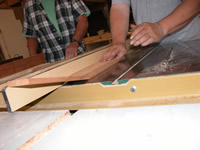 |
When completed, the truss rod is tested in the roughed-out neck. |
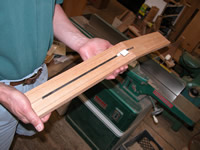 |
The patterns for the neck and the head are traced on the stock,
and the neck is rough-cut (shaping will occur after gluing up the
fretboard). The off-cuts from the neck were used to add the "ears"
on the head--the ears are small decorative scallops on each side
of the head. |
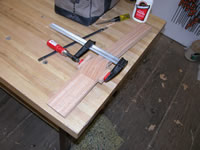 |
Elapsed time for these steps:
4 hours... See the main page for the
cumulative time. |
|
Two veneers--one of maple and one of ebony are placed
on top of the head and are glued in place. This will form a decorative
and protective cap on the head. |
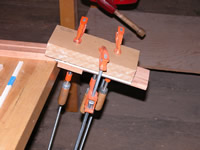 |
Using cut-offs from the original neckboard, a hell
is assembled and rough-sawn, using the bandsaw, to the eventual shape
of the heel. |
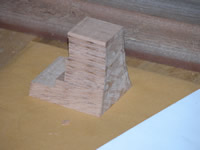 |
Once the head cap veneers are rough sawn and the heel
is glued in position (the part of the heel that will contact the
guitar is at the 14th fret), the neck is ready for placement
of the fingerboard, shaping and carving, and placement on the guitar
body. |
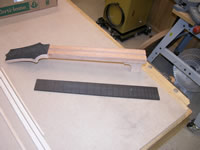 |
I carefully clamped the fingerboard in place on
the roughed neck, then drilled dowel holes. Note that I "flagged"
the
drill bit so that I wouldn't exceed 1/4" depth of hole in the neck.
I drilled two sets of dowels--one at the first fret and one set
at the twelfth fret. I used a 1/16" drill bit (I first measured
my frets
to make sure that the 1/16" hole would be covered by the fret.)
Then, I snipped the head off of some 16 gage wire nails, which
I measured
would just fit within the 1/16" holes. Once clamped in place, I also
marked the fourteenth fret (visible in the photo), which I used
to trim off the end of the neck.
|
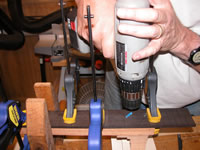 |
Here's a view of the resulting doweling. |
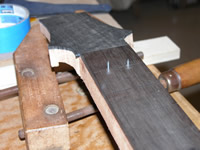 |
Elapsed time for these steps:
7 hours... See the main page for the
cumulative time. |
|
Now, the neck must be fit at the proper angle for the
strings to have good action on the fingerboard. This begins by ensuring
that the body is perfectly flat at the location where the neck will
be joined. I used a scraper to get this area flat. |
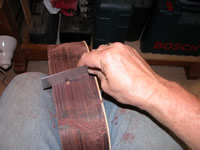 |
To help in determining the proper angle, I constructed
a jig with a small runner that will fit within the truss rod slot.
The jig is about 2" longer than the distance between the nut and
the bridge on the guitar. |
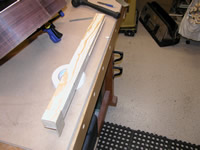 |
I marked the bridge end of the jig at the scale length
as shown (plus 1/8" for "compensation"), and used double-sided
tape to place a 1/8" shim
on the underside.
When set correctly, the neck (without the fingerboard in place) should
be angled so that there's a 1/8" gap between the end of this
jig and the soundboard, which the shim indicates. |
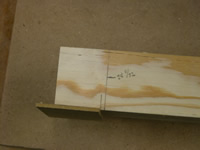 |
As can be seen on this photo, the neck angle doesn't
allow the jig to be fully seated. The heel of the neck (where it
meets the guitar body) must be angled slightly so that the jig may
be fully seated along the
length
of
the neck. |
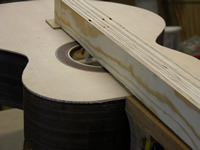 |
I marked the appropriate angle, and rough-sawed the
angle using my band saw. |
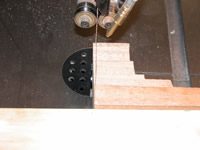 |
I then fine-tuned the heel angle, using a well-sharpened
block plane and a sanding block. I worked carefully to avoid rounding
the edges of the heel. Once the heel was very close, I decided I
needed to complete the body before further fine-tuning. I will check
the heel again once I've installed the heel bolt, carved the heel,
and closed up the body. Each of those steps may slightly change the
neck/body fit. |
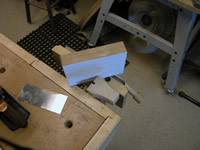 |
Elapsed time for these steps:
8 hours... See the main page for the
cumulative time. |
|
Now, I turned my attention to installing the heel bolt.
I have already drilled the hole for the heel bolt in the body assembly,
shown here without the back installed. |
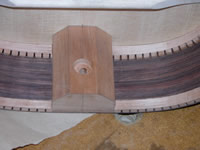 |
To begin planning, I measure the distance that the
threaded bolt insert will protrude from the guitar body, and add
about 1/8"--this will become the depth of the hole I drill in the
heel. |
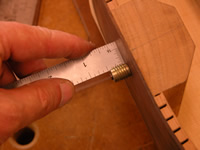 |
I traced the image of the insert hole on the bottom
of the heel. Dan Biasca suggested drilling and gluing a dowel into
the heel to provide a stronger joint at the bolt insert. I laid out
where the drilled hole will go, keeping the hole approximately 1/8"
back from the edge of the heel. I've decided to install a 1/2" dowel. |
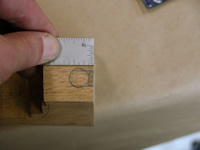 |
The depth of the dowel will extend just beyond the
3/* hole that I will drill for the brass threaded insert. I drilled
the hole using my drill press. |
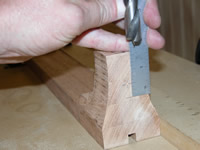 |
I decided that I would like to keep the dowel wood
the same as the heel--mahogany. So, rather than buy a 1/2" hardwood
dowel, I turned a 1/2" dowel out of some scrap mahogany that was
leftover from my heel block. |
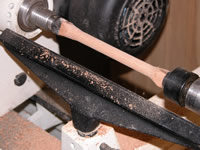 |
I then epoxied in the dowel. I used epoxy, since it
has gap-filling properties, and my dowel was just slightly smaller
than the drilled hole. |
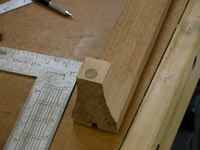 |
I clamped the neck in place and re-marked the location
for the brass threaded insert, by using my 5/16" brad point bit. |
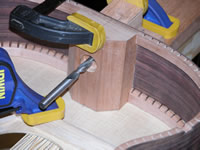 |
I then drilled the hole for the brass insert. At this
stage, though, I made an error that I later had to correct. I drilled
the hole slightly angled, rather than perpendicular to the heel surface.
Later, when I tried to bolt things together, I had to ream out the
bolt hole to accommodate the poor drilling. |
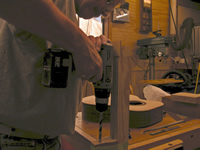 |
Finally, I used soap to lubricate the threads of the
insert, and I screwed the insert into the heel. |
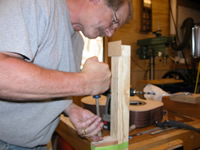 |
For the first time, I could now bolt the neck to the
body. |
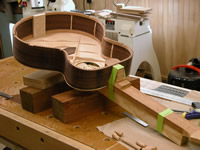 |
Elapsed time for these steps:
5 hours... See the main page for the
cumulative time. |
|
Now its time to get the neck in better shape, so that
I can glue on the fretboard. I want to do some better shaping of
the heel and head, so that I can re-check the fit with the guitar
before I glue up. I've used the templates to lay out the curve of
the heel, and am removing most of the waste with the bandsaw. |
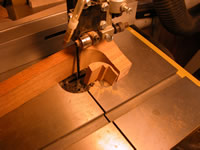 |
Next, I begin by chiseling out a close representation
of the final curve of the neck near the heel. I don't want to carve
the entire neck, so that I have a flat surface for gluing on the
fretboard. |
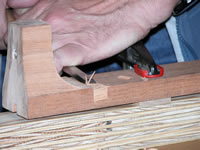 |
Once I have carved out the neck curve, I can rough
in the shape of the heel. I roughed this in with a carving gouge. |
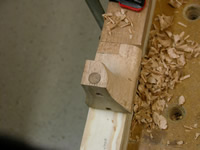 |
I then attacked the other side of the heel. The heel
is now very close to final shape. |
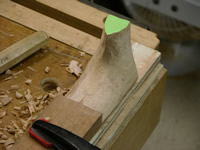 |
I repeat the same process for the head-neck connection,
starting with an approximate curve for the neck. |
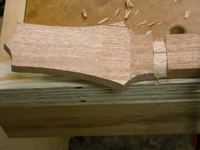 |
Then I again use a carving gouge to rough shape the
head-neck connection. |
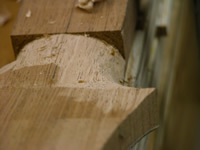 |
Wow! there really is a guitar neck in that block of
wood. |
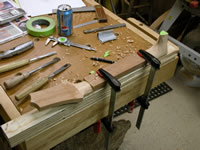 |
Before I glue up the neck, I want to cut the slot for
adjustment of the truss rod and install the truss rod itself. I marked
the location of the slot, then drill out the curved end, and used
a saw to cut the slot, finishing up the slot with some small chisels. |
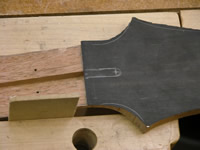 |
I placed the truss rod in position to check that the
Allen wrench will fit properly. Everything looks OK. |
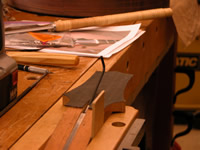 |
I secured the truss rod in place with some silicon
glue, securing the two ends at the nuts of the truss rod. I let this
cure overnight. |
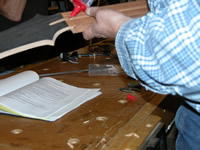 |
The neck, with truss rod in place, is now ready for
installation of the fretboard. |
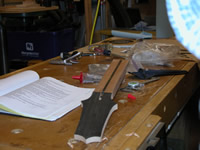 |
I began installation of the fretboard by gluing the
nail dowels that I had made earlier. I used superglue to secure the
nails in the holes, the clipped them if to about 1/16" long. I cleaned
up any extra superglue so that the surface is flat. This will provide
a way to register the fretboard in the right location when I glue
it up. |
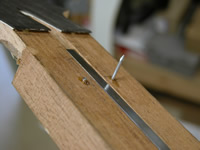 |
I apply Titebond glue to the neck. This will be the
last time that I see the truss rod. |
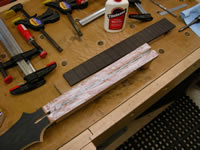 |
Using a caul to help distribute the force of the clamps,
and to avoid damage to the fretboard, I clamp the fretboard in place. |
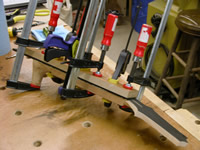 |
With the fretboard now glued, I need to radius it.
I build a template with two radii--14" for the crown at the 19th
fret, and 12" for the crown at the 0 fret. |
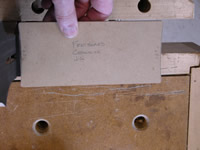 |
I then begin the process of crowning the fretboard.
First, I thin the fretboard by 1/16" from the 0 fret to the soundhole.
Then I cut the crown using a plane. As the crown is cut, I deepen
the fretslots to avoid losing them (I previously prepared my Stanley
keyhole saw to use as a fret saw--described to photos down).. |
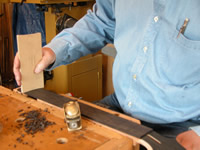 |
The finished, crowned fretboard--cut using the plane,
and a sanding block of 120 and 220 grit paper. |
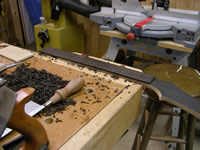 |
To cut the fret slots, I needed to adjust my Stanley
keyhole saw. I made several adjustments. First, I adjusted the kerf
of the saw by placing the saw blade between two pieces of steel and
then hitting the blade with a hammer. My goal was to reduce the kerf
to about .023". Then, I used a triangular file to change the rake
angle of the teeth. The teeth of the new saw had a strong forward
rake angle, which caused difficult sawing. So, with the triangular
file, I filed each tooth to have a slightly negative rake angle.
This made the sawing mush easier and reduced my worry of chipping
as the saw exited the slot. |
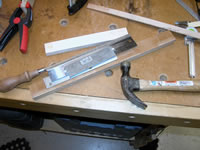 |
Further, I built a jig to limit the depth of the sawn
slot to about 0.10, which is slightly deeper than the depth of the
tang on the fret material I purchased from LMI.
I had to look on LMI's website to find the exact dimension of the
tang depth. |
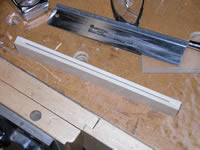 |
The jig is simply two pieces of hardboard cut about
1-1/2" long than the saw blade, and put together with a couple of
shims on each end so that the saw blade will just pass through, but
so that the back of the saw will not. The jig is measured to allow
the blade to only be exposed at about 0.010". This will prevent me
from overcutting the frets. |
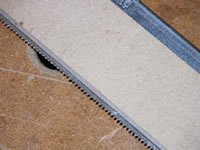 |
I then use the fretsaw and jig to re-cut the fretslots
to depth. I found that the narrow slots would bind easily with the
fine ebony dust. I solved this problem by frequently applying wax
to the saw blade--which made a great difference. |
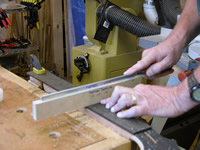 |
With the fret slots cut, I established a curve for
the soundhole end of the fretboard. |
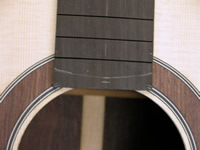 |
I then clamped the neck and fretboard and sawed the
curve, finishing it with a sanding block. There is about 1/16" of
soundhole exposed. |
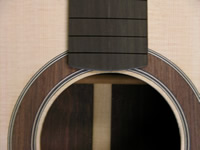 |
My next task was to do the almost-final shaping of
the neck. To accomplish this task, I could have used a chisels and
planes,
but instead I chose to use my shaving horse. I began by using a draw
knife to get the neck to its rough shape. |
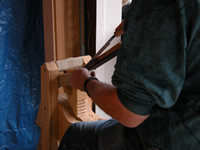 |
I followed the shaping with, in succession--a spoke
shave, a file, and 60-100-150-220 grit sand papers. I worked on the
shaft first, and then followed with final shaping on the neck and
the head. I made the thickness of the neck/fingerboard to be 1" at
the 9th fret, and at just under 7/8" at the 1st fret. |
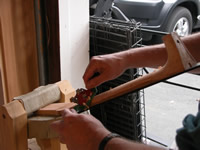 |
The almost final, shaped neck. |
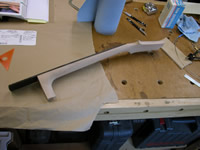 |
Here's a shot at the heel. I worked hard to keep a
defined line at the apex of the heel, running it as far as I could
to the neck shaft. Note that the dowel that I drilled earlier is
off-center. Thank goodness this'll be hidden by the heel cap. |
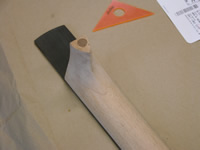 |
Here's a shot of the head. I kept the ears just slightly
tapered. |
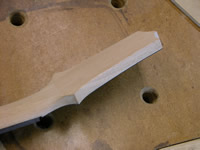 |
With the neck shaped, I cut the slot for the nut. The
nut I received from LMI was 1/4" thick, so I had to sand it down
to 3/16". This is very hard material, so I had to use a power sander
to reduce its thickness. I marked the cut by placing the nut next
to the fretboard, and marking the cut line with a knife. |
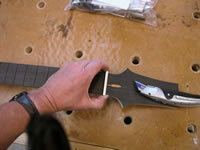 |
I then used a very-fine toothed backsaw to make the
final cut, and cleaned up the channel with a chisel. |
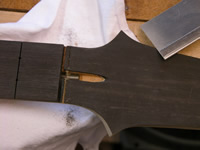 |
To bore the holes for the tuning machines, I used the
template for the head, with lines marked for the locations of the
holes. I checked the dimensions on my tuning machines, and determined
that the center of the pegholes should be 7/16" of an inch from the
edge of the head. This will leave about 1/8" from the edge to the
edge of the tuner on the back of the head. I also measured the tuner
and determined that I needed a 13/32" hole to accommodate the tuner
shaft. After a trip to the hardware store for this odd-sized bit,
I was ready for drilling. |
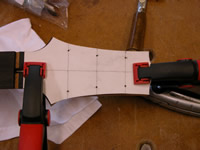 |
Using a backer to avoid tear-out, I placed the head
on a block so that it would lie flat on my drill press table. I then
carefully aligned each hole with the bit, and drilled with the brad
point bit. |
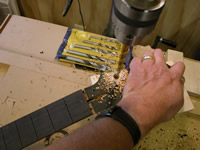 |
The pegholes came out well. Here, I've temporarily
installed one of the tuning machines to make sure that everything
fits. So far, so good! |
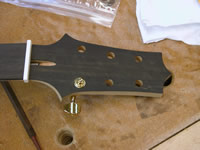 |
Elapsed time for these steps:
12 hours... See the main page for the
cumulative time. |
|
I need to install the dots on the front of the fretboard,
however, I'd like to use the drill press to do so, so I need a way
of holding the now curved neck horizontal. To solve this problem,
I made a "saddle" to hold the neck. I needed to put a curve into
a piece of softwood (I used a pine 2x4 piece), so I placed a straight
edge (I used my level) on a skew on the table saw, and slowly raised
the blade in 1/8" increments until I approximated the curve of the
neck. |
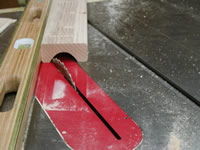 |
Then, I lined the curve with a thin layer of cork.
I then placed the neck into this saddle and went to the drill press
to drill the first hole for the Mother of Pearl fretmarker. |
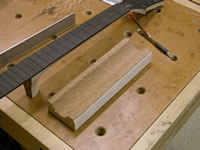 |
It was very difficult to control the depth of the drill.
The first hole I drilled was too deep, so I super-glued a thin wafer
of ebony in the bottom of the hole before I placed the dot. I used
thick superglue to glue the base of the dot, and once placed, I used
thin superglue to lock it in place. I used the same process for each
of the dots, ensuring that the Mother of Pearl dots were slightly
pround of the fretboard surface. Once glued, I used a combination
of files and sandpaper to bring teh dots to the same level as the
fretboard. |
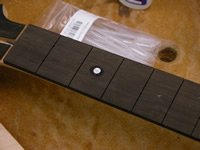 |
Once I installed all of the dots (one dot each behind
the #3, 5, 7, 9 frets, and two behind the 12th fret), the neck had
a very finished feel. |
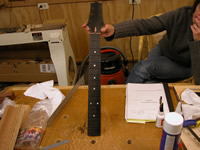 |
Elapsed time for these steps:
3 hours... See the main page for the
cumulative time. |
|
To build the heel cap, I laminated a thin piece of
ebony to a piece of curly maple. I carefully made sure that the end
of the heel was flat and perpendiculr to the fretaboard, and would
be properly positioned in relation to the binding. I used a hardwood
caul (shown) to help distribute the clamping pressure. |
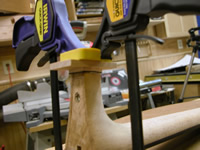 |
Once the glue had dried, the actial heel cap I assembled
was slightly oversized. |
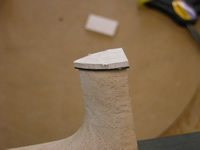 |
Using my shaving horse to stabilize the situation,
I refined the shape of the neck at the heel area. |
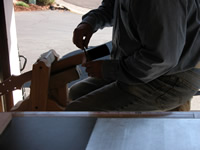 |
The final neck heel is looking pretty good. Note that
I held the heel away from the back of the guitar by about 1/8" or
so. |
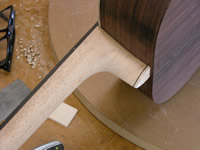 |
Elapsed time for these steps:
4 hours... See the main page for the
cumulative time. |
|
I hadn't installed the side fret-marking dots when
I installed the fingerboard fret markers, because the dot stick
(a 6" white plastic rod) that I received from LMI was
2mm in diameter. Although there's a fractional bit (3/32") that's
very close, when I tested the fit on scrap it felt too tight, so
I sent off for a 2mm bit (none were available locally). When I received
the bit, I drilled approximately 3/16" deep holes at the same locations
of the front dots. I cut small, 1/4" pieces from the dot stick and
used needle nose pliers to place the piece into the hole--in which
I had put just a small amount of thick superglue (CA glue). Once
placed I put a touch of thin superglue over the dot to allow the
glue to wick along the length of the dot. |
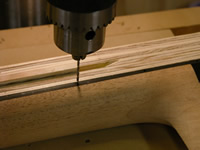 |
Once placed. I carefully filed the dots down to the
side of the fretboard. The fretboard side will be further filed later,
so I didn't spend too much time getting them exact. Here's a shot
of the dots after the frets were installed, which I did next... |
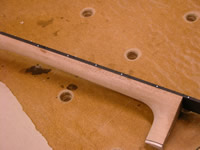 |
Elapsed time for these steps:
2 hours... See the main page for the
cumulative time. |
|
I began the process of installing the frets by cutting
the individual pieces out with a pair of end-cutters. I purchased
a 48" length of fret material from LMI, which came wrapped in a circle.
This circle wrapping preserved the curvature of the fret material,
which is important so that the frets secure to the fingerboad securely.
I laid the material over the fretboard at each fret position, and
cut the frets about 1/8" to 1/4" oversize. To keep track of which
piece went where, I placed a piece of masking tape, adhesive side
up, on the bench and put the fretpieces on it in order. In the photo,
the top piece is fret #1. |
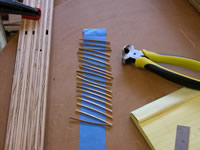 |
I gathered what I'd need to install the frets, includingsome
water, a small glue brush, glue and a brass hammer. I have the neck
placed in the caul that I made earlier. Oh--not shown is a wet, folded
paper towel. |
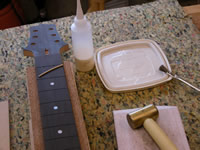 |
To secure the frets, I used the brush to place a small
amount of water into the fret slot, then put three small dots of
glue over the slot as shown. As you can see, the glue tended to thin
out and run some in the slot, which I wanted. Then using the paper
towel, I wiped of the excess and then placed the left end of the
fret in the slot and tapped it down with the brass hammer. I then
tapped down the opposite end, and proceeded to hammer the fret in
by working toward the middle. |
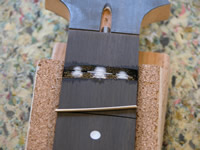 |
Here are several of the frets installed. As I continued
this process, I learned that I was hammering too gently. Initially
I was afraind of hurting the frets, but the frets were not being
seated fully. With more force, they seated more securely. I was glad
that I had built the caul earlier. |
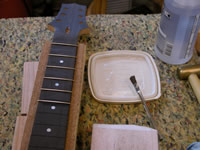 |
After each fret was installed, I checked to see whether
the fret was laying properly in the slot. If not, I went back and
re-hammered it until I was satisfied. Also, I learned that the previously
installed fret may have loosened a little due to the hammering, so
I also checked back a fret or two. |
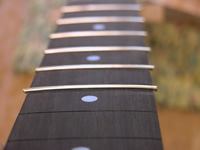 |
Where the fingerboard was nailed to the neck, there
was ample support for the fret hammering. On the body end of the
fretboard, however, there needed to be additional support, so I shimmed
it underneath with blocks and continued the fret installation. |
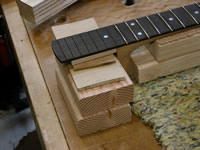 |
Once installed, the result looked great. Now I'll let
it dry overnight and work some on the body before I attach the neck
to the body. |
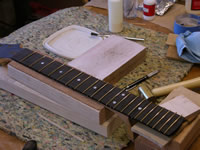 |
Elapsed time for these steps:
3 hours... See the main page for the
cumulative time. |
|
I attached the neck to the bobdy of the guitar and
checked the fit. I carefully adjusted the fit between the neck/heel
and the guitar body. |
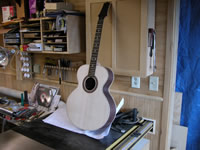 |
Before I assemble the neck to the body, I decided to
do some of the rough fretwork by filing the edges of the frets to
about a 35-degree angle, as suggested by Jonathon Kinkead in his
"Build Your Own Acoustic Guitar" book. This is the last of the work
that I'll do on the neck before attaching it permanently to the body.
After it's attached, I'll level and final shape the frets. |
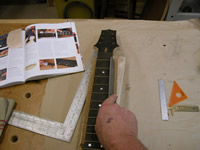 |
Elapsed time for these steps:
1 hour... See the main page for the
cumulative time. |
|