The neck is done, except for fret leveling and finishing, which
I can only do after the neck is attached to the body. The body is
done, except for attaching the bridge, which I can only do when the
neck is attached to the body, So...I guess I need to attach the neck
to the body! To provide for clamping, I built these three clamping
cauls and lined them with cork so that I wouldn't damage the guitar
parts.
Before gluing, I also carefully cleaned up the top, heel, and
heel-side of the guitar. |
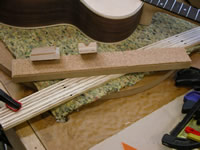 |
I spread glue on the guitar-side of the fingerboard, and carefully
bolted the neck in place, then used the cork-lined cauls to clamp
the neck in place. I checked, re-checked, and double-re-checked to
see that everything was well-placed. |
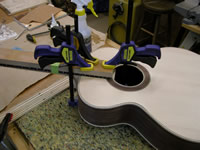 |
Here, you can see the heel fit on the left side of the guitar. |
 |
Note how the clamping caul with the "vee" notch was used to protect
the soundhole brace while clamping the fingerboard. |
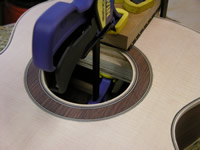 |
Finally, the right side of the heel block where it meets the guitar.
Things look great. |
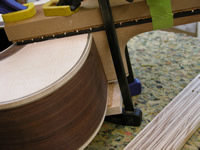 |
Since everything looks OK, I added a second clamp at the soundhole
and now I'll leave the assembly to sit overnight. Can't wait to get
those clamps off. |
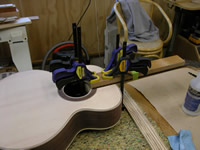 |
Clamps are off, ready for adjusting the frets... |
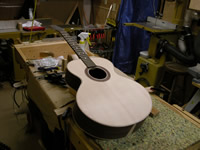 |
Elapsed time for these steps:
2 hours... See the main page for the
cumulative time. |
|
To start adjusting the frets, I first check the frets
for level. I discovered that a couple of the frets are slightly high. |
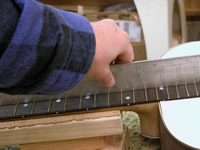 |
In addition, I checked to see that the neck angle is
still properly set. Here, I have placed the bridge in approximately
the right location, and placed my straight edge on top of the frets.
There is a slight gap between the straight edge and the top of the
bridge. This should work well when finally tuning the guitar. |
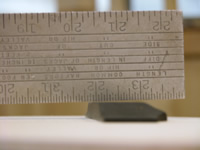 |
I started the fret leveling process by carefully filing
down the high frets (it didn't take much--just a few strokes of the
file). Then, I ensured that the frets were level from one to the
next. I did this by using a fine, single-cut file across several
frets at a time. This leveled the frets, but created a flat spot
on top of each fret. |
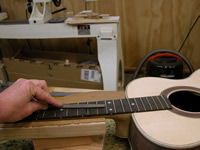 |
When the frets were leveled, I needed to re-round the
frets. I use a fine-cut triangular file to re-round the frets. However,
those files are serrated on the edges, so to protect the fingerboard,
I ground the tips of the "triangle" smooth on my grinder, as you
see. This was suggested by the Jonathon Kinkead book, and it worked
very well. |
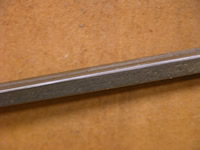 |
I carefully moved from fret to fret, re-rounding each.
Here, I am working on fret. The other fret you see has been rounded
on the top. |
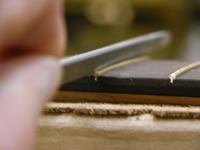 |
Also, I adjusted the ends of the frets at a slight
angle, so that the guitar will be more "playable"--i.e., it won't
hurt the hand to press the string against the frets. To protect the
guitar top, I cut a protective caul out of some scrap formica. |
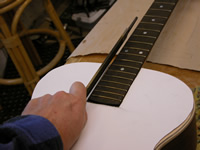 |
Finally, after all of the filing, I polished the frets
using progressive grits of sandpaper--400, 600, 800, 1200. Maybe
a little touch up will be required later, but they look pretty good
now. |
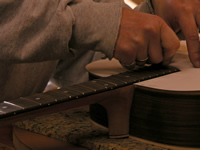 |
Elapsed time for these steps:
3 hours... See the main page for the
cumulative time. |
|
Another detail before finishing--applying an inlay
to the headstock. I drafted a graphic representation of my favorite
Cascade volcano--Mt. Jefferson. Then, I cut out a model of the artwork
in formica, temporarily installed the tuning machines, and used stick-glue
to place the formica template on the headstock. This way, I could
visualize the finished condition, and plan the final placement. Based
on the trial, I decided to slightly reduce the final inlay from that
shown. |
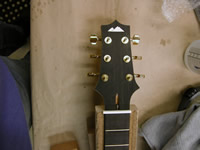 |
I recut a new inlay template in the adjusted size,
and then re-cut a formica template in the new size. I obtained some
figured mother-of-pearl inlay blanks, traced out the pattern, and
used a jeweler's saw to cut out the two pieces of the inlay. |
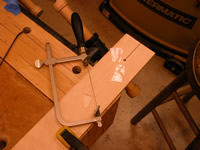 |
To lay out the inlay on the neck, I placed a piece
of double-stick tape on the headstock, drew my lay-out line and placed
the inlay pieces in the final location. Then I carefully used an
Exacto knife to trace around the inlay. When done, I used the knife
to remove the inlay pieces, pulled up the tape, and highlighted the
knife-score with a pencil. |
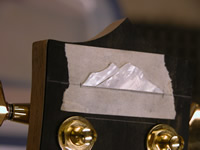 |
I then prepare to rout out the inlay area. First, I
had to rig up a means to hold the guitar neck steady while I worked
on the inlay. Here, you can see how I did just that. |
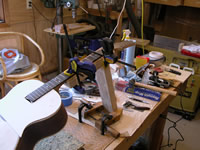 |
Then using a router set up with a Dremel tool and a
1/8" router bit, I carefully routed as much of the figure as I could.
Working very slowly, I could rout right up to the lines. |
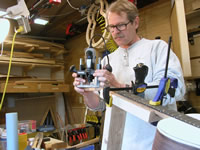 |
Of course, the 1/8" router bit couldn't clean
out all of the tight corners, so I use some very small chisels to
complete
the inlay mortise. I used a magnifying hood to help me with this
close work. The ebony was very brittle and I had to be vary careful
not to accidentally chip the edges. |
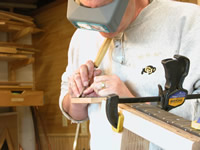 |
I colored some epoxy with epoxy colorant. I had earlier
test using ebony dust with epoxy, but I didn't like the coarse nature
of the epoxy after adding the dust. The epoxy colorant didn't add
to the thickness of the epoxy, which I liked. |
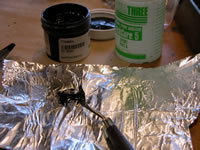 |
Here's a shot of the piece epoxied in place. I use
5-minute epoxy, and let the piece set for about four hours to harden.
The colorant appeared to slow down the setting process, so I wanted
to allow ample time for curing. |
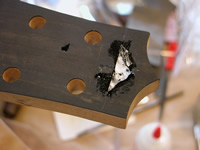 |
Finally, I used a small, fine flat file to reduce the
mother-of-pearl inlay down to the level of the ebony. |
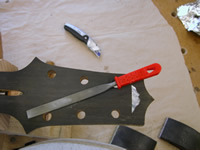 |
Finally, I sanded lightly with 150 and then 220 grit
paper. The result is a very neat inlay. This will look wonderful
beneath the finish. |
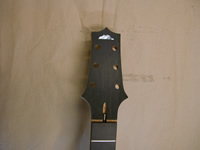 |
An additional detail--I worry about the neck bolt vibrating
loose, so I used a little thread-locking compound to help secure
the neck bolt. To install this, I clamped the heel to the guitar
body, removed the bolt, applied the compound (shown) and re-installed
the bolt. I was careful not to get any of the compound on the inside
of the guitar. |
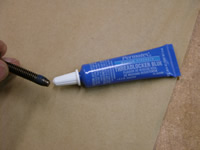 |
It's my birthday!!!!!!! And so, I'm a year older than
when I started the guitar. My gift was a guitar case, in which I
have placed the unfinished guitar. It's great; I can keep the guitar
safe while I figure out the finishing... |
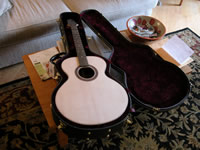 |
Elapsed time for these steps:
5 hours... See the main page for the
cumulative time. |
|